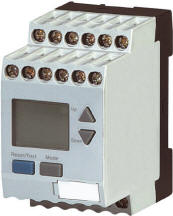 |
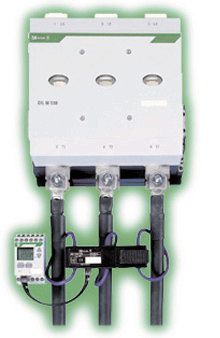 |
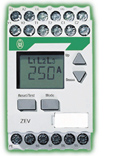 |
Setting Range of Overload Trip Amps |
For Use with: |
1 - 820 |
DILE(E)M To DILM820 |
Moeller’s ZEV electronic overload relay
offers the ultimate motor protection at an economical price.
The base unit protects against overloads, phase failure and
phase imbalance in motors from 1 to 820A. Thermistor
connections and optional ground-fault protection make the
ZEV a great choice for virtually all applications where
sophisticated, yet economical motor protection is required.
The new standard in protection
Newly-developed sensor systems and tripping units make the
ZEV electronic overload
relay the “top-of-the-range” in motor protection. Enhanced
tripping classes provide reliable protection for motors with
run-up times as long as 40 seconds. Trip classes are
selectable from 5 to 40 seconds, allowing precise protection
for a range of applications.
Additional features and options
Optional core-balance transformers detect ground faults
quickly, while an integrated
thermistor connection makes it easy to upgrade to a full
motor-protection
system.
Easy to operate
A built-in LCD guides you through set-up and operation. In
the event of a fault, the display indicates the origin –
speeding the process of troubleshooting and repair.
Configurable auxiliary contacts may be added for
communication of ground faults, thermistor trips, internal
faults or early warning of an overload.
Flexibility for multiple environments
The multi-voltage module automatically adapts to different
voltages from 24-240V AC/ DC, providing a fast and flexible
connection to all conventional control.
Compact design
Ring-type current sensors make the ZEV a great choice for
protection of even small motors. There’s no need for main
current wiring or back pan drilling. The sensor is
installed quickly and easily with hook & loop fasteners.
Compared to conventional transformers, this design is up to
58 times smaller, saving valuable space in the control
panel.
Safety and approvals
The ZEV electronic overload relay is touch safe to IP20
specifications. It meets approval
standards of UL, CSA, IEC/EN 60 947 and VDE 0660.
|
Ordering Instructions |
A complete ZEV Electronic Motor Protective
Relay consists of:
ZEV Electronic
Motor-Protective Relay |
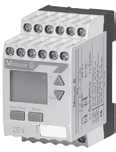 |
Adjustable Setting Range |
Length mm |
Diameter mm |
For use with.. |
Part Number |
1 – 820 |
-- |
-- |
DILEM
DILM7 – DILM820 |
ZEV |
Current Sensors |
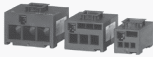 |
1 – 25 |
-- |
6 |
DILEM;
DILM7 – DILM25 |
ZEV-XSW-25 |
3 – 65 |
-- |
13 |
DILM32 – DILM50 |
ZEV-XSW-65 |
10 – 145 |
-- |
21 |
DILM65 – DILM115 |
ZEV-XSW-145 |
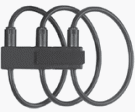 |
40 – 820 |
-- |
110 |
DILM185 – DILM820 |
ZEV-XSW-820 |
Connecting Cables |
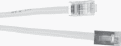 |
-- |
200 |
-- |
ZEV-XSW-25
ZEV-XSW-65
ZEV-XSW-145
ZEV-XSW-820 |
ZEV-XVK-20 |
-- |
400 |
-- |
ZEV-XVK-40 |
-- |
800 |
-- |
ZEV-XVK-80 |
SSW Core-Balance Transformers
(for ground-leakage monitoring) |
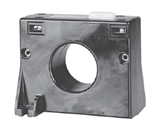 |
-- |
-- |
40 |
-- |
SSW40-0.3 |
-- |
-- |
-- |
SSW40-0.5 |
-- |
-- |
-- |
SSW40-1 |
-- |
-- |
65 |
-- |
SSW65-0.5 |
-- |
-- |
-- |
SSW65-1 |
-- |
-- |
120 |
-- |
SSW65-120-0.5 |
-- |
-- |
-- |
SSW65-120-1 |
Mounting Adapter |
 |
Enables screw
mounting of ZEV and
Current Sensors to
back pan |
ZEV
ZEV-XSW-25
ZEV-XSW-65
ZEV-XSW-145 |
ZB4-101-GF1 |
|
Circuit for Manual Restart |
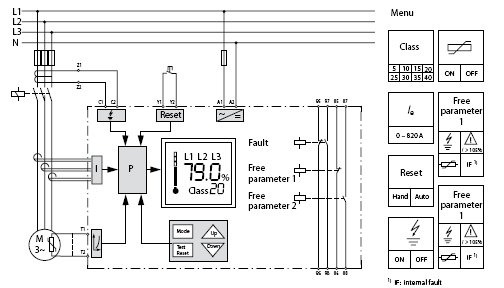
Inputs |
Outputs |
A 1 / A 2 |
Rated control voltage |
95 / 96 |
NC contact for overload / thermistor |
T 1 / T 2 |
Thermistor sensor |
97 / 98 |
NO contact for overload / thermistor |
C 1 / C 2 |
SSW core-balance transformers |
05 / 06 |
NC contact freely assignable |
Y 1 / Y 2 |
Remote reset |
07 / 08 |
NO contact freely assignable |
|
Switchgear and cable sizing corresponding to the
respective starting inertia (CLASS) |
The switchgear is designed for “CLASS 10” in
normal and overload operation. To ensure that the switchgear
(circuit-breaker and contactor) as well as the cables are
not overloaded with extended tripping times, they must be
over-dimensioned accordingly. The rated operational current
Ie for switchgear and cables can be calculated with the
following current factor while taking the tripping class
into account:
Tripping Class |
Class 5 |
Class 10 |
Class 15 |
Class 20 |
Class 25 |
Class 30 |
Class 35 |
Class 40 |
Current factor
for rated operational
current Ie |
1.00 |
1.00 |
1.22 |
1.41 |
1.58 |
1.73 |
1.89 |
2.00 |
|
Relays with integrated sensor |
With the ZEV-XSW-25 to ZEV-XSW-145
push-through sensors, the motor supply leads for each phase
are pushed through the respective push-through openings. On
motor currents which are less than 1 A, the motor supply
leads with the ZEV-XSW-25 are inserted in loops. The number
of loops depends on the rated motor current involved.
Number of Loops n |
4 |
3 |
2 |
Rated motor current IN [A] |
0.31 - 0.4 |
0.41 - 0.62 |
0.63 - 1.24 |
Current settings on relay IE between lowest and
highest value [A] |
1.24 - 1.6 |
1.23 - 1.86 |
1.26 - 2.48 |
The current setting IE of the device is calculated as: IE
= n x IN
|
Recovery time after trip |
Class |
5 |
10 |
15 |
20 |
25 |
30 |
35 |
40 |
trecovery after overload trip [min] |
5 |
6 |
7 |
8 |
9 |
10 |
11 |
12 |
trecovery after test button trip [sec] |
5 |
5 |
5 |
5 |
5 |
5 |
5 |
5 |
|
ZEV PDF AWA |
|
ZEV Dimensions |
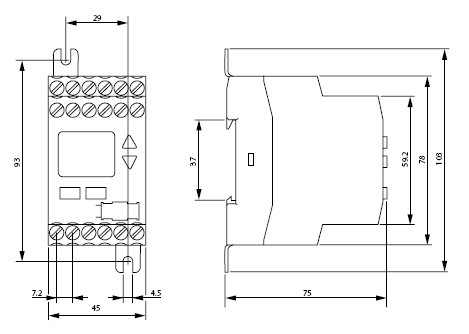
|
|